No, this article is not about forging documents. It is about the medieval art of forging a blade from steel. Yes, knife making has been a highly skilled trade for many years. The ancient Japanese art of sword making perfected design elements. They fold the steel over a thousand times to ensure the blade will not break!
The legend is that you can slice a man in half with a samurai Katana sword. As farfetched as that may seem, the craftsmanship of the Katana might bring some truth to the folklore. Many a limb have been lost because of that sword.
There are two ways to make a knife. There is forging, and there is grinding. In forging, you heat steel to glowing red temps and hammer the steel into the shape you want. Like I said: Samurai swords are repeatedly folded. And, well, that adds strength. Ever wonder why your car has lines in the panels? Strength.
When you heat steel, you heat treat it. Heat treating changes the composition of the steel, which strengthens it. The process hardens molecules in the steel, also making it more corrosion resistant. Too high of a heat treatment will make the steel chip or roll or snap and shear off. Too low of a heat treatment will hinder sharpening. The perfect mix is necessary!
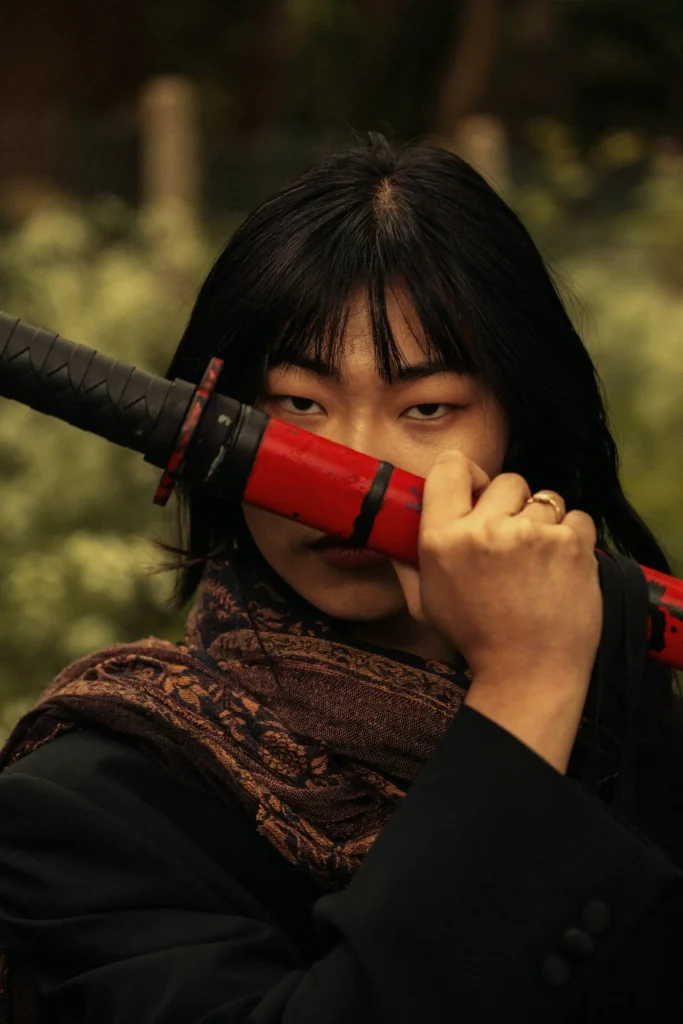
You have to consider edge geometry in your blade’s design. The thinner the edge, the better slicer it will be. The grind also must be considered. A hollow grind is great for combat knives. A shallow grind will cut most things like a hot knife through butter. On a Samurai sword, a tanto edge makes a strong piercer. The Samurai used two swords in combat. The shorter one, the tanto, was more of a dagger and used for very close fighting. A Scandi grind aka a Scandinavian knife is a zero-degree grind that makes it easy to get the angle. This knife is especially suited for carving wood because it is very sharp and easy to sharpen.
A lot to know, right? This is just a fraction of knowledge.
A few years ago, I wanted to make knives. I started with wood. I’d draw a design on paper, stencil it onto a piece of wood, and cut out what is called the blank. Once the blank is cut, you start grinding it on your belt grinder, tempering it down to the width you want and smoothing it out. Once you grind the blank, you put the plunge grind in and then grind the edge in. Now, to heat treat a blank, you use a kiln and then drop it into oil, or you can sub-zero quench it in dry-ice water. The heat up and then quick freeze hardens it.
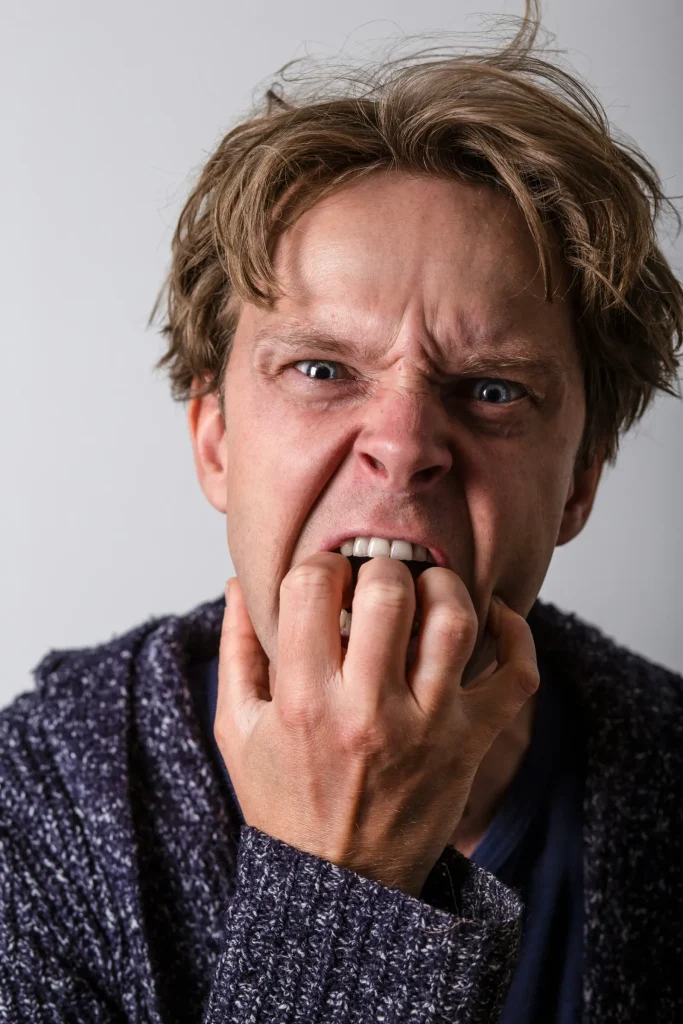
I never got past making wooden knives. It is very expensive to become great at knife making. It takes heavy machinery. And making mistakes in wood is a lot cheaper than ruining steel. Let me tell you: YOU MESS UP A LOT!! Plus, for me, if I’m going to use steel, I will want to go with a top tier metal. With wood, you mess up, you throw it in the fire pit and start over. With steel, you mess up, you have a useless paperweight. Furthermore, it’s entirely possible to cut twenty-five blanks just to make one decent knife. That’s way more paperweights than anyone needs.
Learning this trade is not cost effective! I got good with a full flat grind on my knives. It’s relatively simple to taper down without lines in the blade and then grind an edge on it. I used a belt grinder for that. I held the knife at an angle and guided it across. If I had gotten into steel knives, I would have needed a sharpening system where I could dial in the angle I wanted and then, I’d need to make swipes with grit stones. You can choose from most abrasive to most fine. You hone the edge to a razor sharpness, then strop it for a polished look. A strop is a leather band for sharpening a razor.
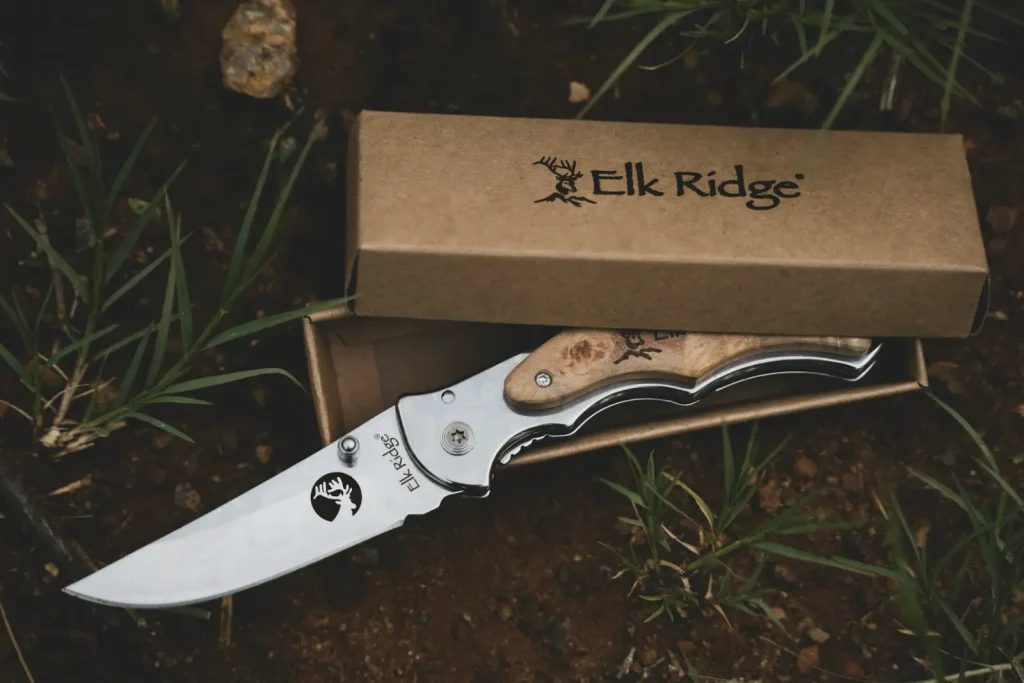
Knives are a big part of my life and lifestyle. My father taught me to always carry a blade. He used to say that it may save your life or someone else’s. But when I see a knife, I see art, a masterpiece of craftsmanship! What has gone into that piece of steel from start to finish requires enormous skill.
If I could work with a professional, I would love to try to make a knife from steel. Maybe, one day, I will. And, maybe, one day, there will be a company with my name on it!